Propelling Pediatric Care
Segal summer interns collaborated with Shriners Children’s Chicago to ensure accuracy of measurements captured by the pediatric specialty hospital’s motion capturing system.
On Chicago’s Northwest Side, sitting across the railroad tracks from a factory that produced Snickers, M&Ms, and Skittles for decades, Shriners Children’s Chicago works to bring a different kind of joy to children and their families.
A pediatric hospital specializing in orthopaedic conditions, Shriners attracts patients from across the Midwest, even the globe, to its campus for expert care. The work of clinicians, therapists, and support staff, including engineers like Adam Graf and Bryana Vasquez in the hospital’s Motion Analysis Center, ignites treatment plans that increase mobility and help children pursue their life’s ambitions.
Last summer, a group of Northwestern University students in the Segal Design Institute Summer Internship program leaned into human-centered design and developed a novel product to help Shriners continue fulfilling its noble-minded mission. The Orthopedic System for Calibration and Angle Review – OSCAR, for short – is a 3D modeling calibration tool intended to validate the patient data Shriners captures from its existing 3D Motion Capturing System.
“We need to trust the numbers we collect [in the Motion Analysis Center] because physicians, surgeons, and other clinicians rely on that data to inform patient care,” Vasquez said.
OSCAR’s origins
Shiners’ current motion capture system records movement and measurements via a series of reflective markers placed on the patient. While the technology, similar to that used in animation and video game development, has proven reliable, Graf and Vasquez wanted to ensure the accuracy of the system’s measurements.
“Double checking these numbers only benefits our patients and their care,” Graf said.
In early 2024, Graf and Vasquez partnered with Segal and, specifically, students in a Design Thinking and Communication (DTC) course for a solution. While each of the four DTC teams devised a unique concept to validate Shriners’ 3D motion camera system, no single prototype answered Shriners’ precise needs.
In the summer, six Segal interns – undergraduates representing three different programs at the McCormick School of Engineering (Mechanical Engineering, Biomedical Engineering, and Manufacturing and Design Engineering) – inherited the challenge of crafting a more robust solution.
The intern group used the DTC teams’ prototypes as a starting point, testing the prototypes and assessing their performance while also evaluating feedback from Shriners stakeholders.
Interns also reviewed project limitations and constraints. With a $400 budget, the device needed to be portable, easily adjustable, durable, and replicate the size of a seven-year-old child. Shriners staff also needed to be able move each joint – the ankles, knees, and pelvis – in different planes of motion. And finally, the solution needed to be compatible with Shriners’ existing software while producing high-resolution results and, above all, accuracy.
Diving into human-centered design
The intern team debated several different ideas before developing its three-in-one prototype: a joint system allowing for movement in three planes, a system to measure movements, and a freestanding anatomical frame.
Sourcing materials from the likes of Home Depot, Amazon, and Grainger, the interns constructed OSCAR of a microphone stand, PVC pipe and connectors, shoulder bolts, machine screws, and other readily available goods. Proportioned to the skeletal structure of a seven-year-old, OSCAR also featured six SLA 3D-printed U-joints of Tough 2000 resin.
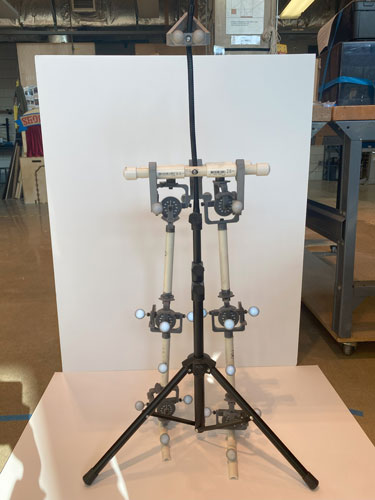
Designed by the team, the joints incorporated a gear-locking mechanism enabling OSCAR to hold its position for precise measurements. The design and material selection of the joints were determined through a MATLAB script written by the team, which simulated failure modes of shear and bending to ensure durability and performance. In addition, reflective markers were placed on all key anatomical positions to integrate with Shriners’ motion capture system.
“We wanted accuracy and something the Shriners team could easily use throughout the day,” said Claire Ortiz-Witter ’26, the intern team’s project lead.
The interns tested their initial prototype and collected feedback from Shriners, particularly noting calls for greater resolution and adjustability.
“The students were terrific at jumping into the project and trialing ideas,” said DTC program co-director Alex Birdwell, who advised the intern team throughout the summer. “They weren’t afraid to revise ideas with feedback and had the determination to keep making the project better until it met all of the project’s requirements.”
After multiple rounds of testing and iteration, the interns presented OSCAR to the Shriners team in September. Both Graf and Vasquez praised the intern team’s progress and persistence.
“The way the students quickly built prototypes, took feedback, iterated, and scaled to a level of complexity really impressed us,” Graf said.
A successful endeavor
While the Segal interns met project requirements, the team’s Handoff Guide presented to Shriners acknowledged ways to further fine-tune the design, including the use of more anatomically correct U-joints and material improvements to the frame construction. Additionally, the team explored the integration of an electronic measurement system to increase accuracy. The intern group documented its work, including circuit diagrams and a detailed GitHub repository for a circuit developed by the team involving IMU (Inertial Measurement Unit) components to capture the Yaw, Pitch, and Roll angles when positioned on a joint.
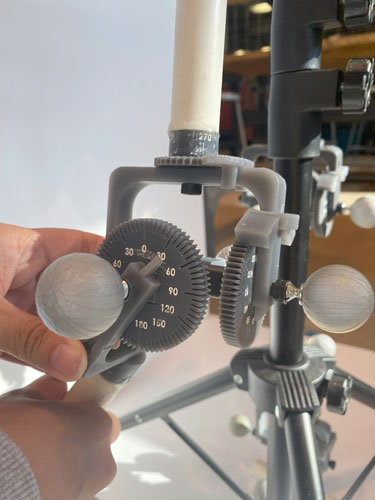
Those potential improvements notwithstanding, Graf has already identified a role for OSCAR at the Motion Analysis Center.
“On an annual basis, we’re required to do different quality assurance checks for accreditation and OSCAR will be a helpful part of that routine,” he said.
In working with the Shriners team, the interns put the human-centered design process into action: deeply working to understand a real-world problem, developing a prototype, accepting feedback, and experimenting with multiple iterations en route to crafting a relevant and capable solution.
“We were an energetic, driven group and that we were able to design something that Shriners feels good about is definitely rewarding,” Ortiz-Witter said.